In product development, speed to market while maintaining quality is critical. That’s why the Circuitwise Group has invested in a major upgrade of its prototyping capabilities by installing a brand-new multi-function pick-and-place prototyping machine. This cutting-edge platform allows product developers to rapidly iterate their designs, allowing testing to detect any errors before committing to volume production.
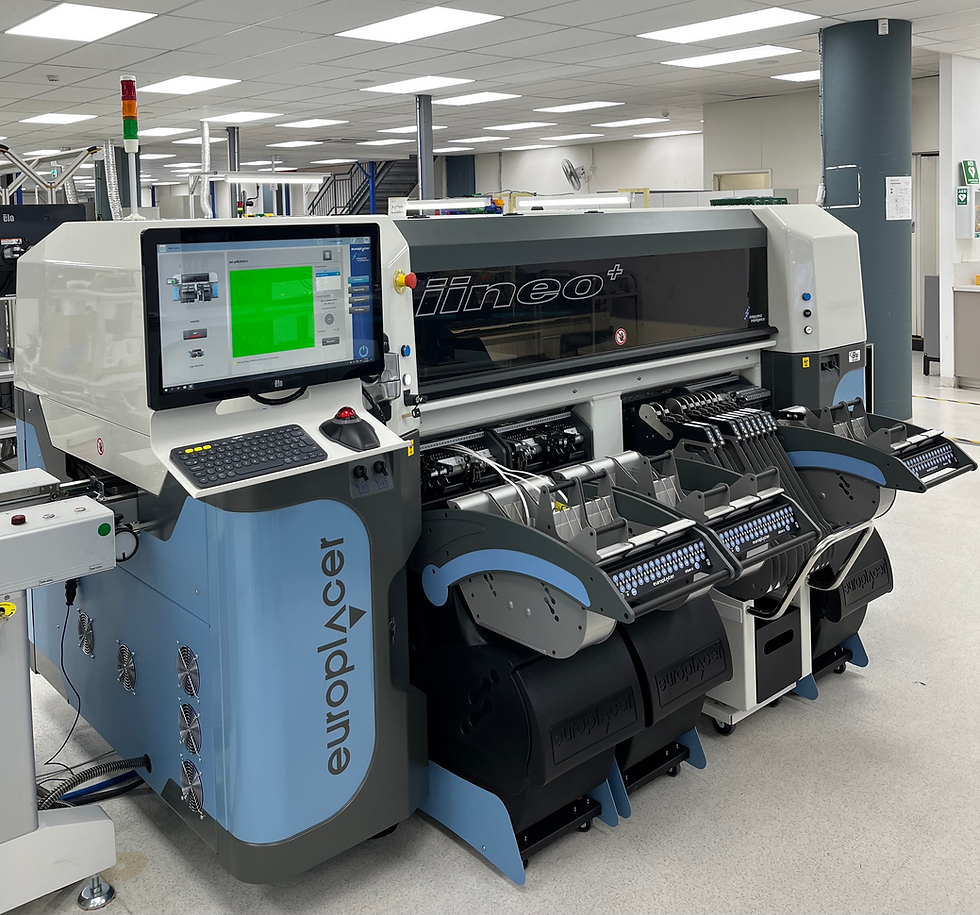
The technology we have chosen is the Europlacer’s inneo+, which has unmatched versatility in the range of components it can handle. In traditional SMT pick-and-place systems, different placement heads may only be capable of handling specific component types, requiring longer setup times. By contrast, the iineo+ has “smart nozzles” that can handle the full range of components, significantly improving prototyping speed.
Design for Manufacture feedback on PCB prototypes
Whether a printed circuit board (PCB) prototype includes standard parts, odd-form components, or intricate designs, Circuitwise can now ensure seamless, accurate placement across all prototype iterations. This versatility allows product developers to push the boundaries of their designs while gaining valuable Design For Manufacture (DFM) feedback from Circuitwise.
Key DFM feedback relates to a range of factors including issues around component placement, manufacturing tolerances, thermal management, assembly line efficiency, soldering quality, testing procedures, BOM optimisation, and process documentation for quality assurance. Prototyping allows the design to be fine-tuned across all these factors and more prior to committing to volume production.
A step up in PCB prototyping capability
As part of our continual improvement ethos, Circuitwise always aims to exceed industry standards to provide the highest quality possible. Our selection of the iineo+ is the latest in a recent series of capability upgrades to put us at the forefront of electronics manufacturing.
The iineo+ delivers almost unlimited configuration options, handling virtually any component and a wide range of board sizes, including large substrates up to 1610mm x 600mm. The platform has a rotary turret head with 12 smart nozzles. The addition of digital vision, integrated intelligence, and linear motors work together to ensure high-speed, high-precision placement for all components.

Several other features support the flexibility and speed. The platform provides 264 positions for 8mm tapes, an internal waffle tray zone for ten JEDEC trays, a built-in component electrical tester, intelligent feeder carts and more. For special assembly applications, options include glue dispense, a fixed camera for large devices, stock management, multi-program optimisation, NPI, and a traceability upgrade option that includes a live production dashboard and auto-width conveyor.
Regarding speed, the winning feature is the ability to “balance” the platform's operation during prototyping. With ordinary prototyping machines, there is always a bottleneck where manual intervention is required due to some limitation. The smart features of this machine and the versatility in component placement mean the platform can be fully balanced for any prototyping run.
Enhancing our obsession with quality in PCB Prototyping
One of the machine’s standout features is its 3DPS (Three-Dimensional Placement Sensing) technology, which offers closed-loop control of the forces applied during component placement. This level of control is critical in ensuring consistent placement accuracy across every prototype iteration, no matter the complexity of the board design.
By eliminating common issues such as component misalignment or improper soldering, Circuitwise can deliver prototypes that are close to what the production version would look like, if not identical. For product developers, this translates into fewer surprises during production and a smoother transition from prototype to final product.
Circuitwise’s installation of the Europlacer iineo+ pick-and-place platform sets a new standard for PCB prototyping in Australia. We have always provided a quality prototyping service, but this investment extends our obsession with quality from the production phase to the prototyping phase. As a partner in innovation, Circuitwise is committed to supporting its customers through every phase of product development.
This equipment was purchased with the support of a Supply Chain Resilience grant from the Australian government.
The Circuitwise Group includes Circuitwise Electronics Manufacturing in Sydney, Australia and Nautech Electronics in Auckland, NZ.
Comments